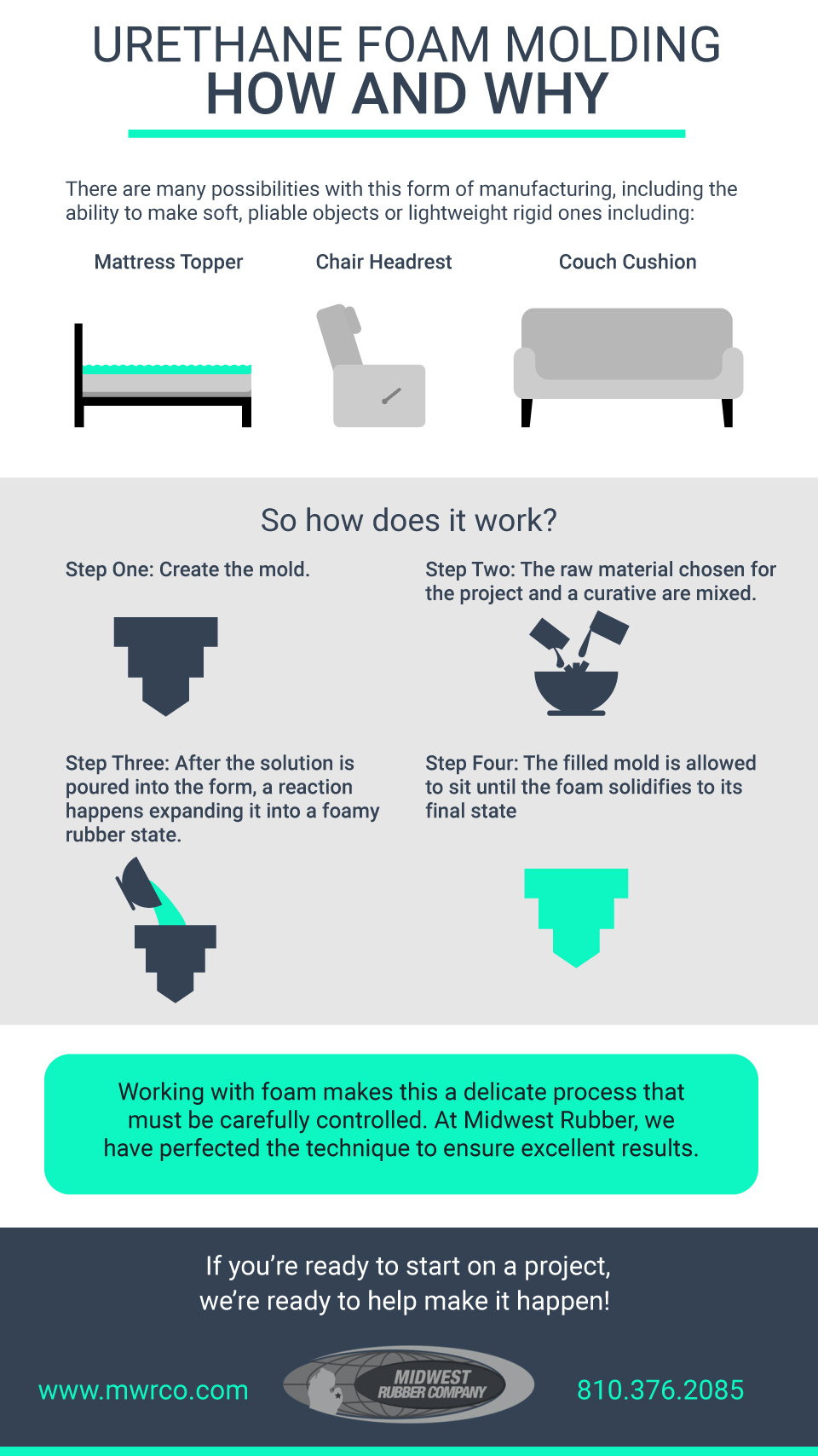
URETHANE FOAM MOLDING
Urethane foam molding is an excellent technique when our clients want to create something with a soft and pliable texture. The use of foam rather than liquid material sets this process apart from our others. Forms for this process are typically made of aluminum, but for intricate shapes we do also utilize flexible silicone forms. By mixing the appropriate components together, a foamy solution results. This can then be inserted into the form, along with any colorants or other materials that need to be included. Sometimes, heat or pressure are applied to change the object’s structure further; in other cases, it is simply left to solidify. The finished item is then carefully removed from the form and ready for any finishing touches desired by the client.
These are some of the advantages offered by urethane foam molding:
- Reliability. The forms used in this technique are typically quite precise, and the completed products generally show a high degree of accuracy.
- Speed. Beyond any branding needs by the client, such as the application of a label, items made through urethane foam molding usually do not need much finishing after they’re completely cured.
- Low cost. Because of its unique properties, one might presume that foam molding is a more expensive process, but that’s not the case. It can actually be a very affordable method.
- Capability. If a light, flexible item is what you need, foam molding is the perfect process.
Urethane foam molding is ideal for creating all kinds of soft items for various industries. Here are some examples of what it may be used to produce:
- Automotive seat cushions
- Molded head cushions for medical use
- Conveyor belt wheels
- Gaskets and seals
If you’re working on a project and need a custom-made part, Midwest Rubber is here to help. We’re ready to put our decades of experience using foam molding and other techniques to use to create exactly what you need for your task. Contact us today, and we can get started.