Midwest Rubber Co. has had the opportunity to work in many different industries because of our reputation for quality and flexibility. We start with meeting the needs of our clients, and we don’t consider our job done until we’ve exceeded their expectations. To achieve that, we rely on processes that maximize the customization we can offer our customers. Let’s take a look at a one of them and see why it’s so effective.
Rotational molding, also known as roto-molding, is a method we use to manufacture hollow objects. It’s an inexpensive alternative to several other techniques that still provides the durable results we demand. It begins with a mold, which is a cast of the shape that the final product will have. We partially fill the mold with the best compound for the job – typically, plastisol or polyethylene. At this stage, this material is either a liquid or in tiny flakes, allowing for more even distribution during melting. The mold is then placed in the oven. As it heats, it is spun on both its vertical and horizontal axes, allowing the now-liquid compound to fill its space entirely and form a complete object. Finally, the mold is taken to a cooling chamber, where we continue to rotate it in the same manner. Once its temperature has dropped sufficiently, it can be removed.
We’re fond of rotational molding because of its reliability, ease, and lower cost for our clients. As a process with wide applicability, we have used it to create products ranging from basic chair components and buckets to more complicated items, like protective boots for trucks and hospital beds. Whenever we need to manufacture something hollow, rotational molding is our go-to procedure.
Rotational molding is one of the many techniques we utilize in our work to bring unique solutions to clients that meet their highly specialized needs. If you’re in need of a custom product or part, contact Midwest Rubber Co. today, and let’s discuss what we can do for you.
Rotational Molding and How We Use It
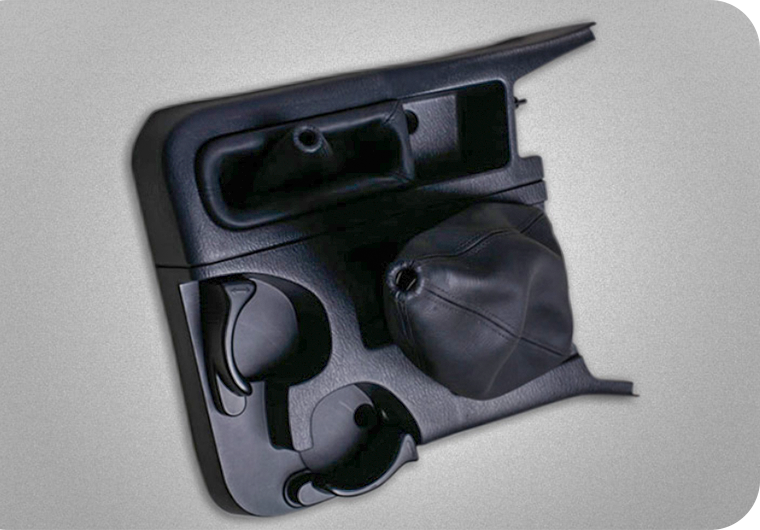